Safety of two roll mills
Two-roll mills, commonly used in various industries, especially in rubber and plastic processing, often consist of horizontally placed metal rolls rotating in opposite directions. The material, typically in the form of rubber or plastic compounds, undergoes mixing, refining, and sheeting processes as it passes through the nip between the two rolls. Despite their efficiency in material processing, the operation of two-roll mills involves intense mechanical forces, and because of this the safety of two roll mills is crucial.
What operators can do to minimize safety risks?
1.
Training and Education:
Before operating a two-roll mill, operators must undergo comprehensive training on equipment handling, emergency procedures, and the importance of safety precautions. Regular refresher courses can help reinforce safety awareness.
2.
Emergency Procedures:
Clearly communicate and display emergency procedures, including the location of emergency stops and shutdown mechanisms. Conduct regular drills to ensure that all operators are familiar with the actions to take in case of an emergency.
3.
Equipment Inspection:
Conduct routine inspections of the two-roll mill to identify any signs of wear, damage, or malfunction. Ensure that all safety features, such as emergency stops and interlocking mechanisms, are in proper working condition.
What we do to minimize safety risks?
State of art safety technology
We implement state of art electronic safety controls and sensors to all our electric two roll mills. Usability always is the starting point.
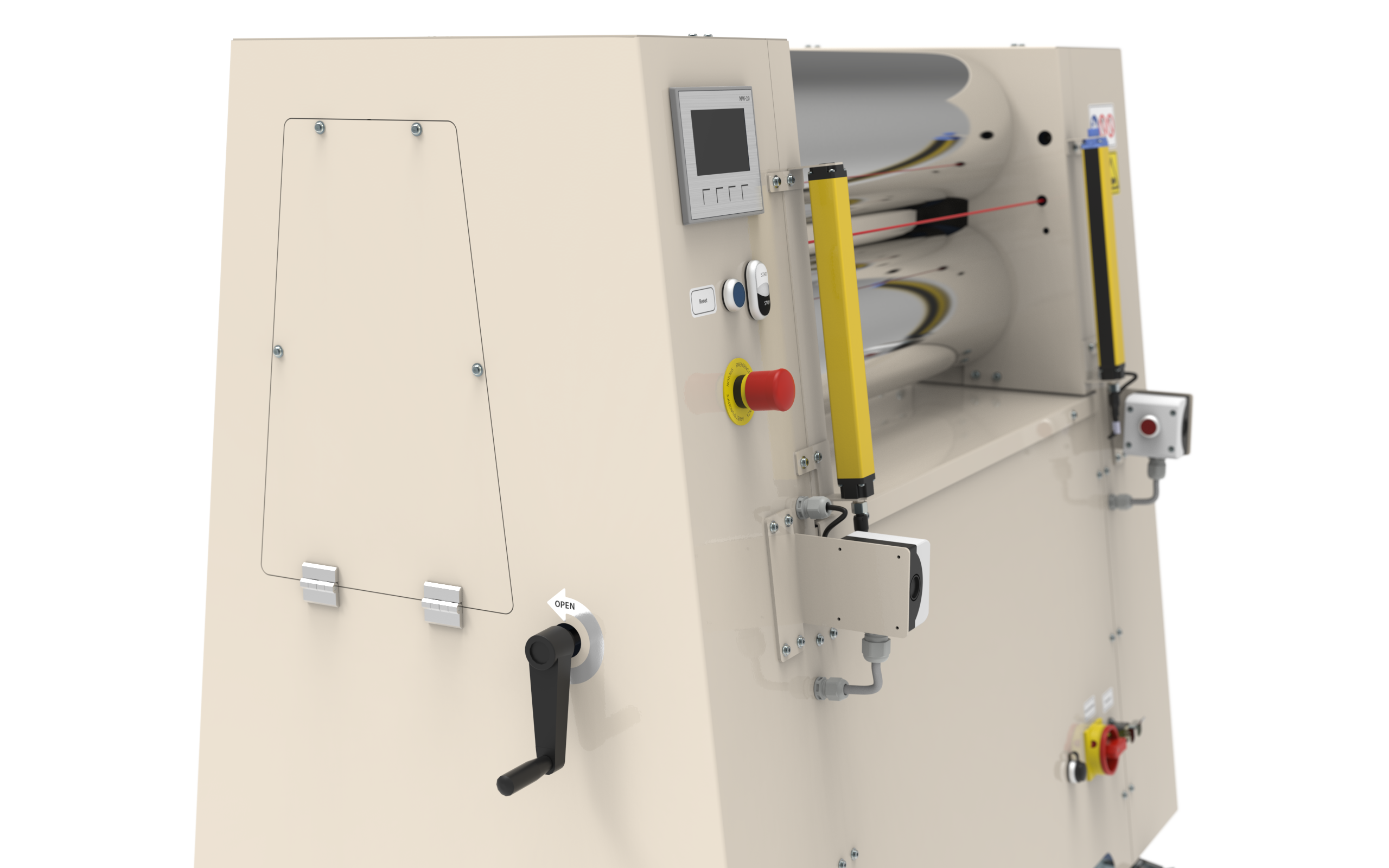
Protective barriers
Where possible and/or required we add protective barriers to the machines. To ensure peak efficiency in your manufacturing workflow, you have the option to tailor the protective barriers according to your specific requirements. Have a look at the customizing options we offer.
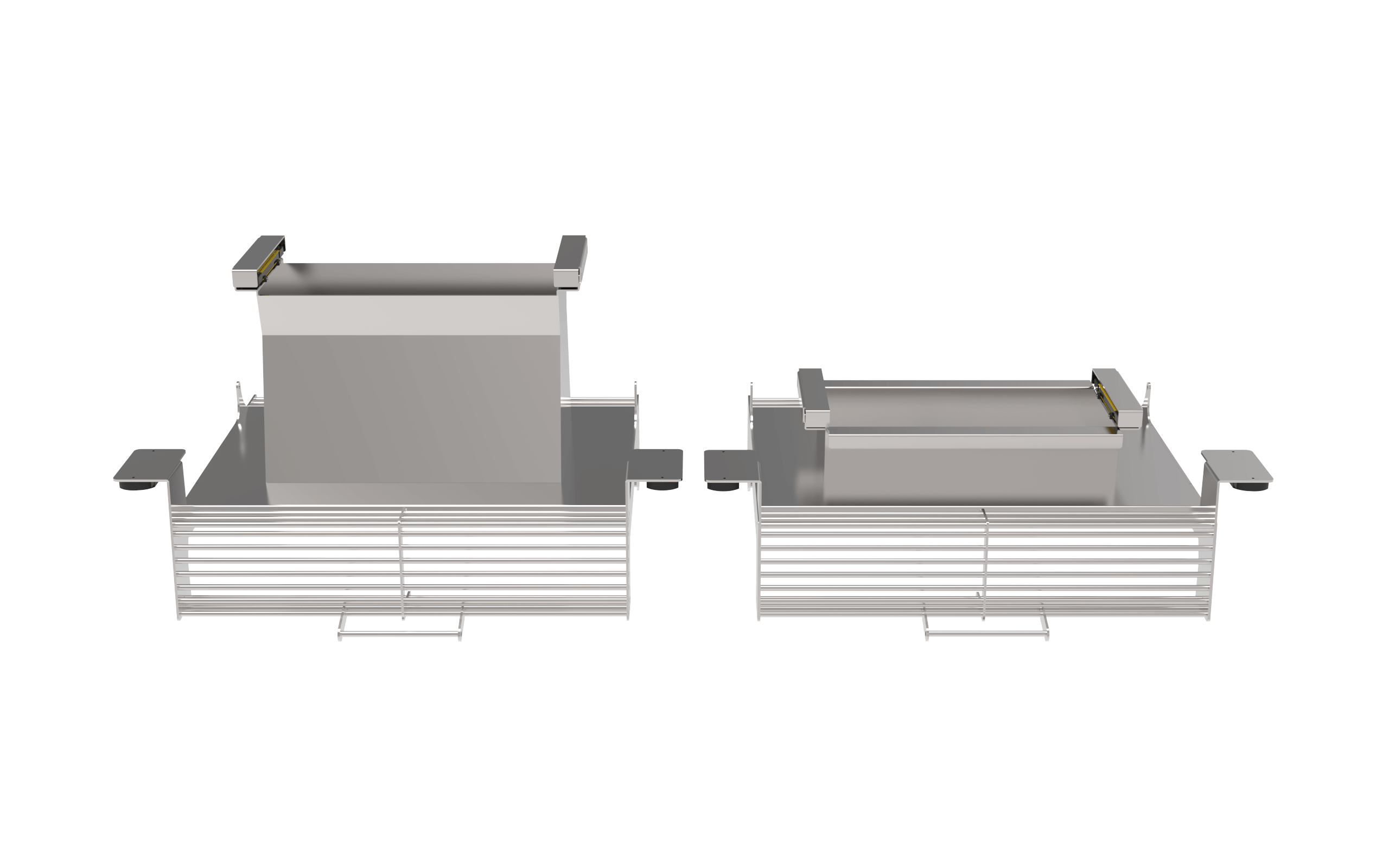
Special cleaning programs
Most accidents happen when cleaning two roll mills. We developed special cleaning programs for all electric rollers to minimize these risks.